Methods of Inventory Management (Cambridge (CIE) A Level Business): Revision Note
Exam code: 9609
The purpose of inventory
Inventory is the goods and materials a business holds for the ultimate goal of resale or for use in production
Types of inventory
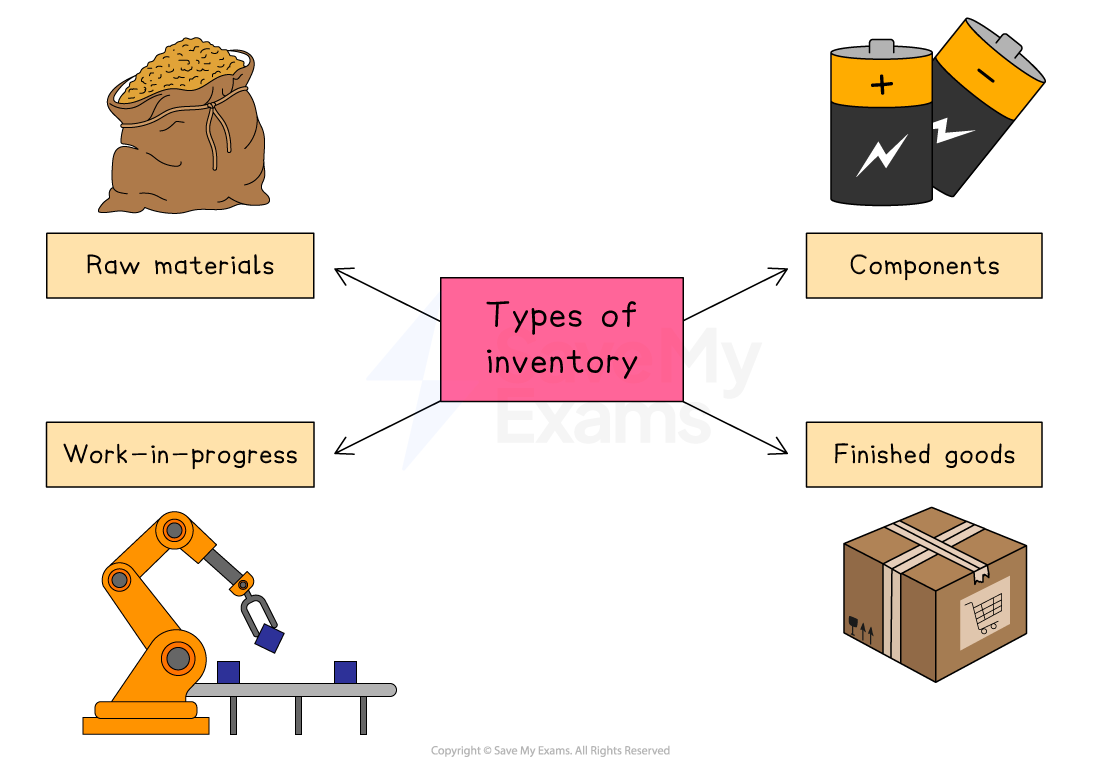
Raw materials | Components |
---|---|
|
|
Work-in-progress | Finished goods |
|
|
Costs and benefits of holding inventory
The management of stock is an important consideration for businesses
Problems may arise from holding inventory
Storage costs (e.g. warehouse rental, security costs) will be higher than necessary
The risk of spoilage and stock shrinkage is increased, leading to increased costs
Money tied up in stock could be used elsewhere in the business
Time and resources are needed to monitor and track stock levels
However, if a business holds inventory, it means that
Products are available when needed, improving customer satisfaction
Buying quantities of inventory and storing it may reduce unit costs due to bulk buying discounts
Production isn't held up by supply issues
Extra stock helps meet peaks in sales, such as during holiday periods
The importance of supply chain management
The supply chain is the network of organisations, people, activities and resources that move a product from its basic raw material right through to the final customer
It includes the following:
Stock control: planning, implementing and monitoring the movement of raw materials, components, work-in-progress and finished goods
Quality control: ensuring output meets standards so that the end product is safe and meets customer expectations
Transport networks: ensuring efficient deliveries of goods to customers, taking account of speed, reliability and costs
Supplier networks: developing strong relationships with suppliers willing to work collaboratively to improve quality
Global supply chains require these activities to be coordinated across international borders
Some stages can be completed at lower cost in certain countries
E.g. China has a reputation for producing high quality, low-cost electronics components
Labour-intensive processing, such as clothes manufacturing, is outsourced to countries with low labour costs, such as Vietnam
Scarce raw materials may only be available in certain countries/regions
Building an effective supply chain
Decision area | What it involves |
---|---|
Make or buy (produce in-house or outsource) |
|
Choosing suppliers |
|
Purchasing approach |
|
Information sharing and use of technology |
|
Logistics structure |
|
Why does an effective supply chain matter?
Faster delivery to customers
When every link is well-coordinated, products move quickly from factory to shelf, beating slower rivals
Lower operating costs
Just-in-time (JIT) deliveries and bulk purchasing agreements reduce storage, handling and material expenses
E.g. Aldi negotiates long-term contracts with a small group of trusted suppliers, helping it minimise warehouse inventory and keep prices low
Consistent quality
Close, long-term relationships with suppliers make it easier to enforce standards and fix problems early
Greater resilience to shocks
A well-planned supply chain includes backup suppliers and effective data sharing so the business can adapt when something goes wrong
Inventory control charts
An inventory control diagram shows how inventory moves into and out of a business over time
An inventory control diagram
The maximum inventory level is the maximum amount of stock a business is able to hold in normal circumstances (1,600)
The reorder level is the level at which a business places a new order with its supplier (800)
The minimum stock level is also known as the buffer inventory level and is the lowest level to which a business is willing to allow inventory levels to fall (400)
Lead time is the length of time from the point of inventory being ordered from the supplier to it being delivered (one week)
The stock level line shows how inventory levels change over the given time period
As inventory is used up, a downwards slope is plotted
When an order is delivered by a supplier, the stock level line shoots upwards
Worked Example
The diagram below shows inventory movements of kitchen shelving units sold by TamFix Limited.
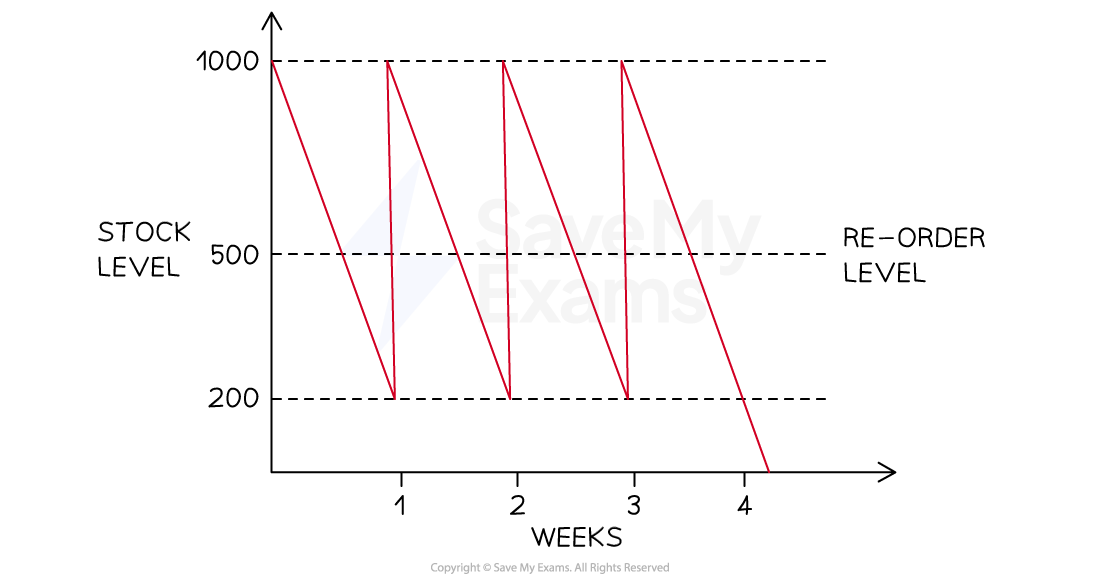
Identify the following points:
The minimum stock level
The reorder level
The reorder quantity
The lead time for kitchen shelving units
(4)
Answer:
Step 1: Identify the minimum stock level
The minimum stock level is identified by the bottommost dotted line
In this case, it shows that the minimum stock level is 200 units (1)
Step 2: Identify the reorder level
The reorder level is clearly identified on the diagram
In this case, it shows that the reorder level is 500 units (1)
Step 3: Identify the reorder quantity
The reorder quantity is the difference between the maximum stock level (shown by the topmost dotted line) and the minimum stock level
The reorder quantity is, therefore, 800 units (1)
Step 4: Identify the lead time for kitchen shelving units
The lead time is the difference in time between the time an order is placed and the time the inventory is delivered
In this case, assuming a five-day working week, the lead time for shelving units is two days (1)
Examiner Tips and Tricks
Always clearly label lead time, reorder level and buffer stock, and include units
Show your workings — examiners award method marks even if the final figure is wrong
Buffer inventory
Buffer inventory is a quantity of stock kept in case of shortages
This can provide a competitive edge over rivals unable to meet demand
This approach is commonly called ‘just in case’ stock control
The decision to keep buffer stocks is one that businesses have to weigh up very carefully
The decision will be influenced by the nature of the business and the product/service it provides
Evaluating the use of buffer stocks
Advantages | Disadvantages |
---|---|
|
|
You've read 0 of your 5 free revision notes this week
Unlock more, it's free!
Did this page help you?