Lean Production (Cambridge (CIE) A Level Business): Revision Note
Exam code: 9609
The aims and purposes of lean production
Lean production is a management philosophy that aims to maximise value while minimising waste
It focuses on maximising efficiency, improving quality and reducing costs
Lean production is likely to lead to a competitive advantage
Lower unit costs are achieved due to minimal wastage so prices may be lower than those offered by competitors
Better quality of output is likely as a result of supplier reliability and carefully managed production processes
The main principles of lean production
Right first time approach
Aim for zero defects in output
Identify and solve problems as they arise
Prevent rather than correct errors
Flexibility
Adaptable capital equipment and physical resources
Multiskilled staff and team working
Flexible management styles
Waste minimisation
Remove processes that do not contribute to added value
Consume as little as is necessary
Rework rather than replace
Effective supply chain management
Develop excellent relationships with suppliers
Minimal number of suppliers
Continuous improvement
Ongoing, small steps
All staff involved in improvement
Lean production strategies
Businesses that pursue lean production can adopt a range of strategies
1. Kaizen
Kaizen means “continuous improvement” in Japanese
It involves small, regular changes made by employees at all levels
Workers are encouraged to suggest ways to improve efficiency, quality and processes
These ideas are implemented gradually over time
A comparison of Kaizen with one-off improvements
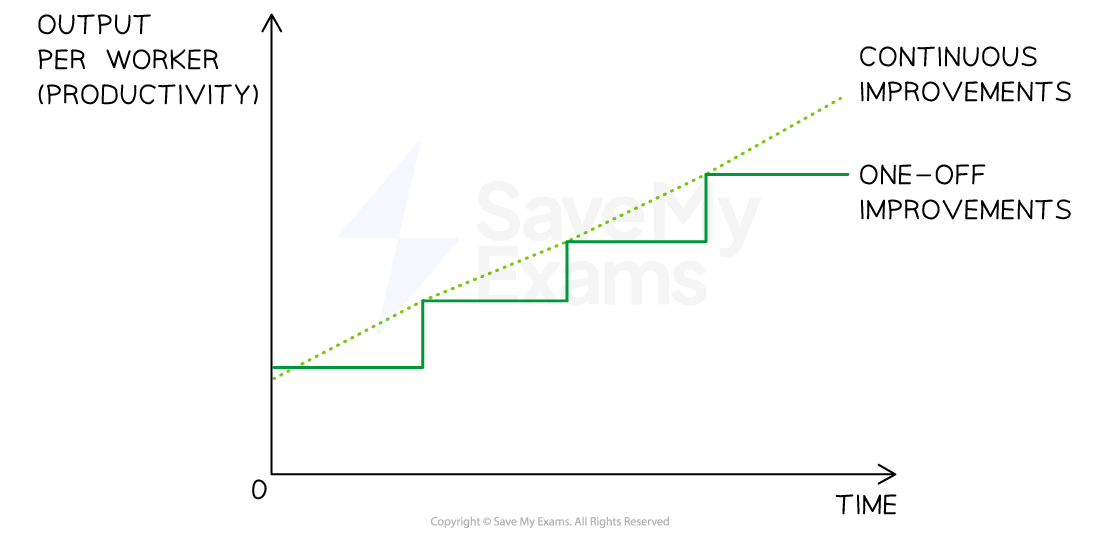
Evaluating the use of Kaizen
Advantages | Disadvantages |
---|---|
|
|
2. Quality circles
Small groups of employees who meet regularly to discuss work-related problems and suggest improvements
These groups usually focus on improving quality, safety or productivity and include workers from different levels of the business
Evaluating the use of quality circles
Advantages | Disadvantages |
---|---|
|
|
3. Simultaneous engineering
A production method where product development stages happen at the same time, rather than one after another
For example, design, engineering and marketing teams work together to reduce the time it takes to launch a new product
Evaluating the use of simultaneous engineering
Advantages | Disadvantages |
---|---|
|
|
4. Cell production
A method of organising production into small teams that complete a whole part of the product process
Instead of passing work along a production line, each cell is responsible for a complete unit of work, encouraging ownership and teamwork
Evaluating the use of cell production
Advantages | Disadvantages |
---|---|
|
|
5. Just-in-time manufacturing
Where products are made only when there is demand, and each stage of production begins only when needed by the next stage
This approach aims to match production with customer demand
This minimises waste, speeds up workflows, and reduces the need for warehousing
Evaluating the use of just-in-time manufacturing
Advantages | Disadvantages |
---|---|
|
|
6. Waste management
Waste can be anything that does not add value, such as overproduction, excess inventory, delays or defects
Lean waste management aims to simplify processes and reduce costs
Evaluating the use of waste management
Advantages | Disadvantages |
---|---|
|
|
The impact of lean production
Lean production affects not only how goods are made but also how people work, how quality is maintained and how inventoryis managed
Lean production impacts
Area of Impact | Explanation |
---|---|
Inventory Control |
|
Quality |
|
Employee roles |
|
Capacity management |
|
Efficiency |
|
Limitations of lean production strategies
Lean production can improve efficiency and reduce waste, but it also presents several challenges and limitations that businesses must carefully manage
Dependence on reliable suppliers
Lean production often relies on just-in-time delivery
If suppliers are late or unreliable, production may stop entirely because there is little or no stock available
Vulnerability to demand fluctuations
Lean systems produce only what is needed
This makes it difficult to respond quickly to unexpected increases in customer demand, which can result in missed sales and unhappy customers
Initial setup costs
Introducing lean production may require investment in new equipment, staff training, and redesigning production processes
These upfront costs can be very high, especially for small businesses
Pressure on workers
Lean production gives employees more responsibility and expects constant improvement
This can create stress or lower morale if staff feel overloaded or too closely monitored
Limited flexibility
Lean strategies work best in high-volume, predictable environments
They are unlikely to be suitable for businesses with highly customised products or irregular demand
You've read 0 of your 5 free revision notes this week
Unlock more, it's free!
Did this page help you?