Methods of Quality Management (Cambridge (CIE) A Level Business): Revision Note
Exam code: 9609
The importance of quality
Quality considers the characteristics and features of a product that satisfy the needs of customers
Businesses need to maintain a level of quality that attracts and retains customers if they want to remain successful
Customer perceptions of quality are related to a range of product or business features
Factors that influence quality perception
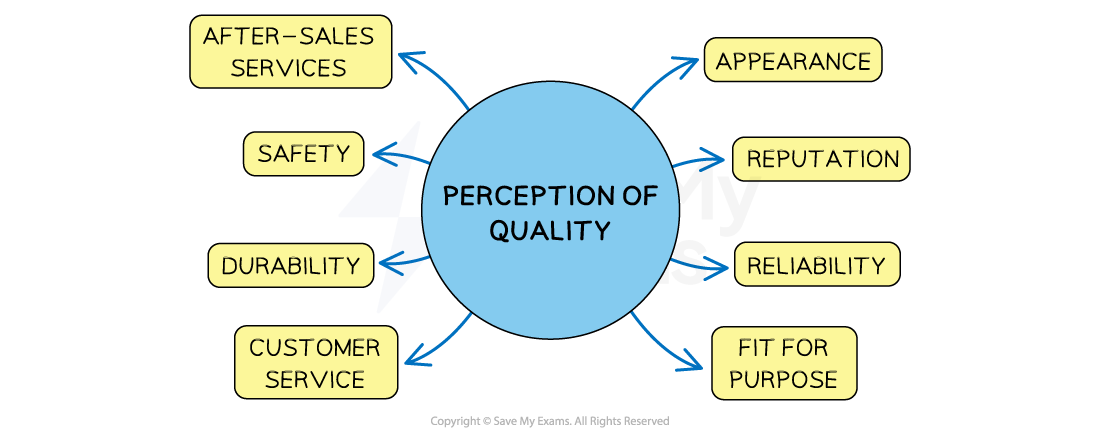
Customers may consider products or services to be of good quality if they
Look good and are sold by a reputable business or brand
Are reliable and durable
Are safe and fit for purpose
Receive good customer service, including after-sales service
If quality is not maintained, then businesses may be at risk of
Losing their competitive advantage and customers to other brands that offer better quality goods or services
Experiencing higher costs due to having to replace faulty or defective goods
Gaining a poor reputation as customers spread poor reviews about the business to others
In some countries laws protect consumers so businesses need to ensure that the products they sell are free of faults or defects to avoid harming customers or their reputation
Quality control
Quality control is a traditional method of checking quality at the end of the production process by using quality inspectors to find faults
It is not possible to achieve perfection in every production process
E.g. there will always be some variation in terms of materials used, production skills applied or reliability of the finished product
The impact of quality control on business
1. Reduces risk of poor-quality products reaching customers
Helps maintain the business’s reputation and avoid customer complaints
2. Wasted output may increase
Faulty items are found after production, so time and materials may already be wasted
3. Higher inspection costs
Employing inspectors adds to labour costs, especially in large-scale operations
4. Low training costs
Limited staff training is needed as inspectors check quality rather than the employees themselves
5. Less responsibility for workers
Employees may depend on inspectors instead of taking ownership of quality themselves
6. Inconsistent quality improvements
Problems are found but not always prevented, so the same issues may continue to occur
Quality assurance
Quality assurance involves inspecting the quality of production throughout the process
Workers check their own work and, sometimes, the work of others throughout the various stages of production
Some business take a whole-business approach to quality assurance, with systems such as quality circles, benchmarking and total quality management
The impact of quality assurance on business
Impact | Explanation |
---|---|
Fewer errors and waste |
|
Improved customer satisfaction |
|
Workers take more responsibility |
|
Training and systems required |
|
Can improve brand reputation |
|
Total Quality Management (TQM)
Total Quality Management (TQM) places quality at its core and makes every worker responsible for quality throughout the business
Quality is considered from the customer's perspective
Inefficiency and wastage is removed from every business activity or function, including those that are not directly related to production
Advantages and disadvantages of TQM
Advantages | Disadvantages |
---|---|
|
|
Case Study
The impact of TQM at Nestlé
Nestlé is one of the largest food and beverage companies in the world, with operations in over 180 countries
With such a large global footprint, consistent product quality and customer trust are essential to its success
Why Nestlé introduced TQM
To maintain consistent quality across its many factories and brands
To improve efficiency in production and reduce waste
To respond better to customer expectations regarding food safety, nutrition, and quality
What changes were made
Nestlé introduced a global quality management system based on TQM principles, including continuous improvement (Kaizen)
It developed a company-wide culture of quality with the slogan: “Quality is the foundation of our company”
It invested heavily in employee training, so every worker understood their role in maintaining high standards
It used customer feedback, regular audits and process checks to improve quality at every stage, from sourcing its raw materials to final packaging
Impact on the business
Area | Impact |
---|---|
Product quality |
|
Operational efficiency |
|
Customer trust |
|
Employee engagement |
|
The importance of benchmarking
Benchmarking involves a business comparing its quality and performance with market leaders within the same industry
1. Internal benchmarking
Comparison of different functions within a business, such as finance or marketing
Performance
Comparison of key performance indicators such as labour productivity or labour turnover rates
Process
Comparison of business operations and processes such as call centre queue times or delivery times
2. External benchmarking
Comparison of key performance indicators, such as the number of product recalls, against those of market leaders in an industry
Evaluating benchmarking
Advantages | Disadvantages |
---|---|
|
|
You've read 0 of your 5 free revision notes this week
Unlock more, it's free!
Did this page help you?