The Importance of Capacity, Efficiency and Productivity (AQA A Level Business): Revision Note
Exam code: 7132
Using capacity efficiently
Efficiency means producing with the fewest possible resources
Using less time, labour, materials or energy
Why efficiency matters
Lower costs per unit
Spending less on inputs increases profit margins or allows lower selling prices to compete better with rivals
Higher competitiveness
Efficient firms can respond quickly to orders, which attracts and retains customers
Better use of resources
Cutting waste frees up cash and reduces a business's environmental impact, meeting both financial and sustainability objectives
Ways to use capacity efficiently
Way | Explanation | Example |
---|---|---|
Streamline the workflow |
|
|
Invest in automation |
|
|
Train staff |
|
|
Introduce just-in-time (JIT) inventory management |
|
|
Preventive maintenance |
|
|
Difficulties increasing efficiency
Improving efficiency in production is not always easy
Difficulties can arise for a range of reasons
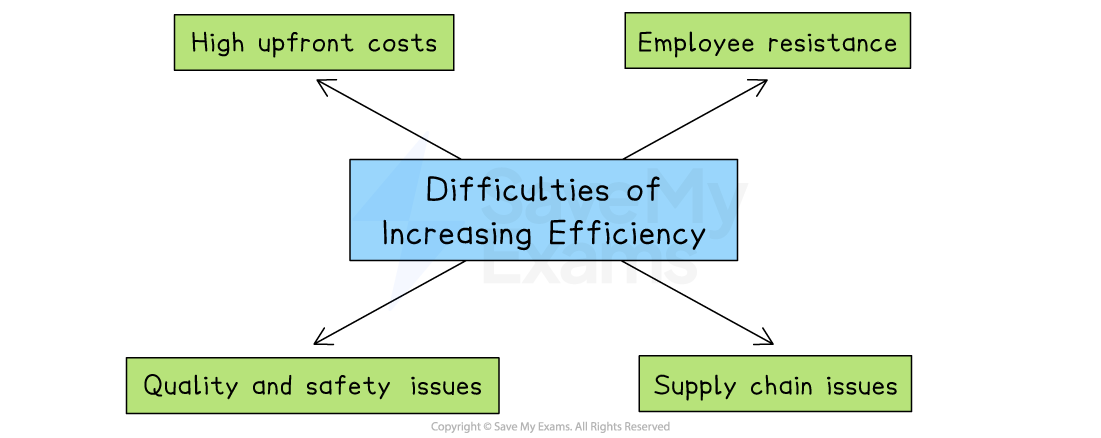
Why increasing efficiency can be difficult
Difficulty | Why it makes efficiency gains hard | Example |
---|---|---|
High upfront cost of new equipment |
|
|
Employee resistance to change |
|
|
Supply chain bottlenecks |
|
|
Quality and safety trade‑offs |
|
|
Efficiency and labour productivity
Labour productivity is the amount of output each worker produces in a given period of time
Higher productivity means the same team turns out more products in the same working hours
Labour productivity is expressed in units and is calculated using the following formula:
Worked Example
Green Man Fisheries prepares a wide range of high-quality seafood dishes that it sells to restaurants. Its most popular product is dressed crab.
Its 12 workers produced 1,404 boxes of dressed crabs in May. In June, the business employed one more worker, and output increased to 1,677 boxes of crabs.
Calculate the difference in labour productivity between May and June.
[3]
Answer:
Step 1: Calculate labour productivity in May
(1)
Step 2: Calculate labour productivity in June
(1)
Step 3: Calculate the difference
(1)
Labour productivity has increased by 12 boxes per worker
Higher labour productivity leads to lower unit costs as long as wage rates remain the same
Worked Example
Each worker at Green Man Fisheries earns £2,000 per month.
Calculate the change in the unit cost of labour between May and June.
[3]
Answer:
Step 1: Calculate labour costs for May and June
(1)
Step 2: Divide labour costs by output for May and June
(1)
Step 3: Calculate the difference
(1)
Unit cost of labour has reduced by £1.59 per box
Ways to increase labour productivity
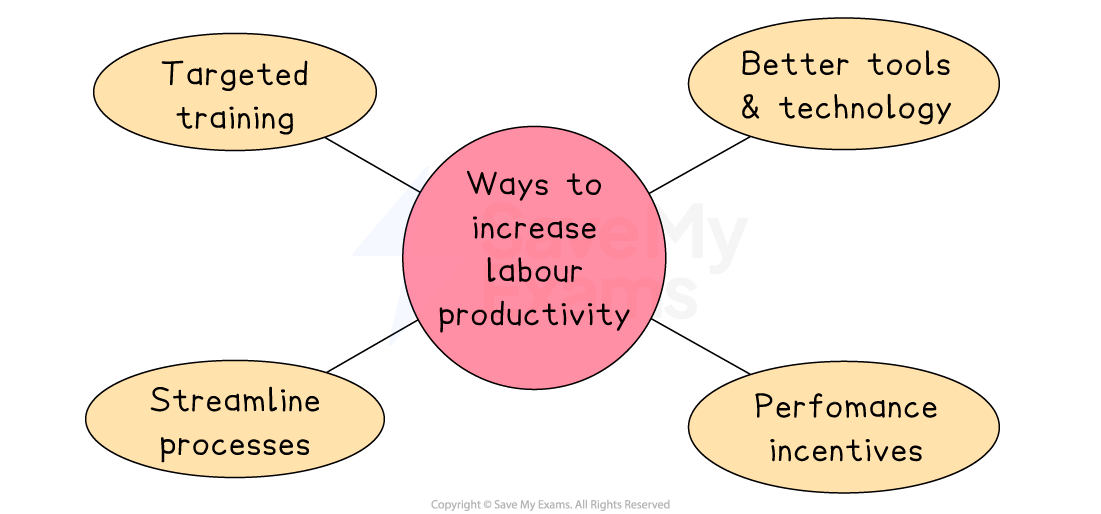
Targeted training
Teach workers faster, safer or multistep techniques so they waste less time and make fewer errors
Better tools and technology
Give employees equipment that speeds up routine tasks
Performance incentives
Link pay or bonuses to clear output targets to encourage extra effort and focus
Streamline processes
Remove wasted steps so workers spend more minutes on value‑adding activity
E.g. Zara reorganised cutting and sewing stages so fabric moves straight to assembly
Difficulties increasing labour productivity
Low morale
Tired, stressed staff work more slowly, are absent more often and make more mistakes, limiting their productivity
Skill shortages
Better tools and methods only help if employees have the right skills
Recruiting or training skilled workers can be slow and expensive
Rigid work rules or union resistance
Employees' contracts may restrict task switching or new performance targets, reducing flexibility and slowing down change
E.g. London Underground’s plans to modernise stations has faced union action, delaying the introduction of multi‑skilled roles and new shift systems
Learning curve for new technology
Installing new software or machines can cut output at first while staff learn and early glitches are fixed
Capital- and labour-intensive production
Capital-intensive production mainly uses machinery and technology in the production of goods and services
Large-scale production of standardised products is likely to be capital-intensive
Manufacturing in developed countries where labour costs are relatively high is likely to be capital intensive
E.g. Car manufacturers such as Ford use robots and other production technology to manufacture vehicles, with supervisors overseeing the quality of output
Labour-intensive production mainly uses physical labour in the production of goods and services
The delivery of services is usually more labour-intensive than manufacturing
In countries where labour costs are low (e.g. Bangladesh), labour-intensive production is common
Small-scale production is likely to be labour-intensive
E.g. UK schools are labour-intensive operations, as teachers plan and deliver lessons and provide pastoral support
Evaluating capital- and labour-intensive production
Type of production | Advantages | Disadvantages |
---|---|---|
Capital intensive |
|
|
Labour intensive |
|
|
Unlock more, it's free!
Did this page help you?