Improving Quality (AQA A Level Business): Revision Note
Exam code: 7132
The importance of quality
Quality products are those whose characteristics and features satisfy the needs of customers
Customers may consider products or services to be of good quality if they:
look good and are sold by a reputable business or brand
are reliable and durable
are safe and fit for purpose
receive good customer service, including after-sales service
Factors that influence quality perception
Many businesses set quality targets to focus staff and resources on meeting customer expectations
Pizza chain Domino's sets targets for home deliveries completed within 30 minutes of customers placing an order
Customers are fully refunded if their pizza arrives after this time
The quality of a business's products can provide a competitive advantage
High levels of quality can be used in promotional activity and provide a unique selling point for businesses in competitive markets
Successfully developing a USP for quality can ease expansion into new markets as a result of the positive reputation it creates
Increased finance may be available to fund marketing activity to improve brand recognition and attract new customers
Quality is closely linked to price
High-quality products can usually command a high price
Lower-quality products may need to be sold at a discount to persuade customers to buy them
Methods of improving quality
Quality control
Quality control is a traditional method of checking quality at the end of the production process by using quality inspectors to find faults
It is not possible to achieve perfection in every production process
E.g. there will always be some variation in terms of materials used, production skills applied or reliability of the finished product
Benefits and drawbacks of quality control
Benefits | Drawbacks |
---|---|
|
|
Quality assurance
Quality assurance involves inspecting the quality of production throughout the process
Workers check their own work and, sometimes, the work of others at various stages of production
Some business take a whole-business approach to quality assurance, with systems such as quality circles, benchmarking and total quality management (TQM)
Benefits and drawbacks of quality assurance
Benefits | Drawbacks |
---|---|
|
|
Benefits and difficulties of improving quality
The quality of a business's products can provide a competitive advantage
Unit costs are likely to be low if a business effectively manages quality
Low costs may allow a business to reduce its selling price to better compete with or undercut its rivals
High levels of quality can be used in promotional activity and provide a unique selling point for businesses in competitive markets
Successfully developing a USP for quality can ease expansion into new markets as a result of the positive reputation it creates
Benefits of improving quality
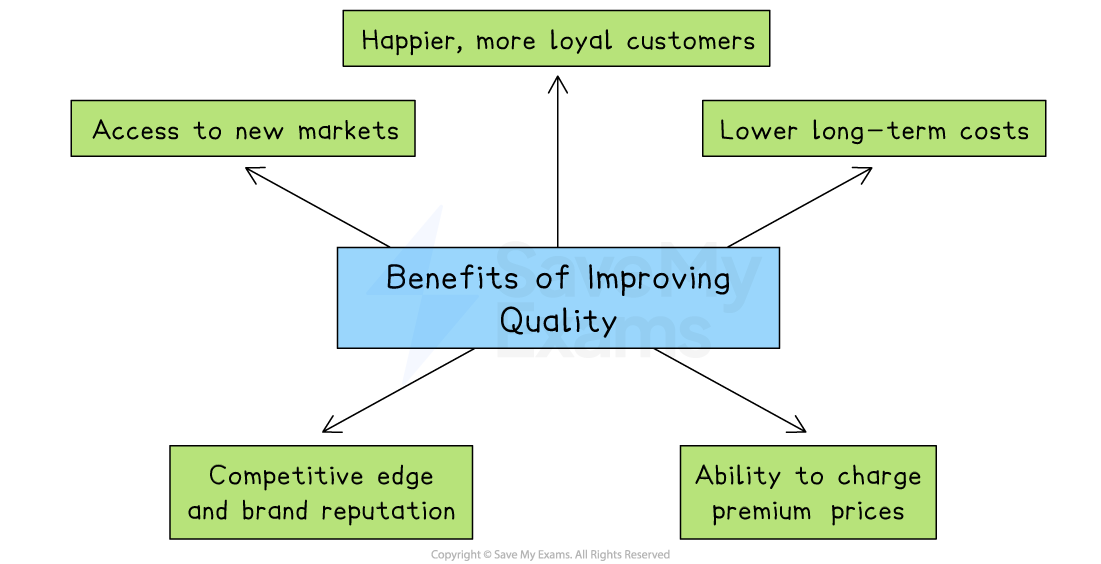
Benefit | Explanation | Example |
---|---|---|
Happier, more loyal customers |
|
|
Ability to charge premium prices |
|
|
Lower long‑term costs |
|
|
Access to new markets |
|
|
Competitive edge and brand reputation |
|
|
Difficulties of improving quality
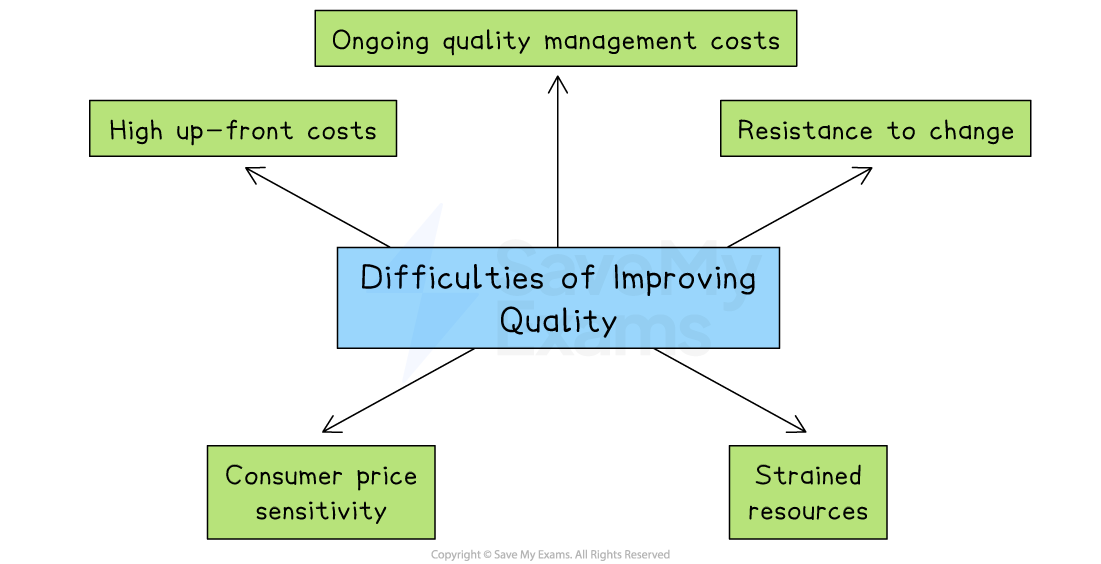
High up‑front and ongoing quality management costs
Small firms often struggle to pay for staff training, better materials and certification fees
Staff or union resistance to new quality systems
Changing routines and adding checks can meet resistance from workers, slowing down their introduction
Customer price sensitivity
Better quality can push costs and, consequently, prices up
Price‑sensitive shoppers may switch brands
Strain on resources
If funds are scarce, pushing for higher quality can overstretch staff and cut service levels
Consequences of poor quality
Poor quality can cause a range of problems for a business
Costly recalls and repairs
Faulty goods must be taken back, fixed or refunded, which can have a significant impact on cash flow and profit
Heavy fines or legal payouts
Safety failures can end up in court, where fines, penalties and compensation bills are huge
Damaged brand reputation and lost customers
News of defects spreads quickly, making buyers switch to rivals they trust more
A sharp drop in sales and profits
Negative headlines can reduce sales and share price, and recovery can take years
Unlock more, it's free!
Did this page help you?