The Supply Chain (AQA A Level Business): Revision Note
Exam code: 7132
Managing the supply chain effectively
The supply chain is the network of organisations, people, activities and resources that move a product from its basic raw material right through to the final customer
It includes the following:
Stock control: planning, implementing and monitoring the movement of raw materials, components, work-in-progress and finished goods
Quality control: ensuring output meets standards so that the end product is safe and meets customer expectations
Transport networks: ensuring efficient deliveries of goods to customers, taking account of speed, reliability and costs
Supplier networks: developing strong relationships with suppliers willing to work collaboratively to improve quality
Global supply chains require these activities to be coordinated across international borders
Some stages can be completed at lower cost in certain countries
E.g. China has a reputation for producing high quality, low-cost electronics components
Labour-intensive processing, such as clothes manufacturing, is outsourced to countries with low labour costs, such as Vietnam
Scarce raw materials may only be available in certain countries/regions
Building an effective supply chain
Decision area | What it involves |
---|---|
Make or buy (produce in-house or outsource) |
|
Choosing suppliers |
|
Purchasing approach |
|
Information sharing and use of technology |
|
Logistics structure |
|
Why an effective supply chain matters
Faster delivery to customers
When every link is well-coordinated, products move quickly from factory to shelf, beating slower rivals
Lower operating costs
Just-in-time (JIT) deliveries and bulk purchasing agreements reduce storage, handling and material expenses
E.g. Aldi negotiates long-term contracts with a small group of trusted suppliers, helping it minimise warehouse inventory and keep prices low
Consistent quality
Close, long-term relationships with suppliers make it easier to enforce standards and fix problems early
Greater resilience to shocks
A well-planned supply chain includes backup suppliers and effective data sharing so the business can adapt when something goes wrong
Modern supply chains
Modern supply chains stretch across the world, rely on real-time data and face tough questions about ethics and sustainability
Businesses now use digital tools, closer partnerships and greener standards to keep those long chains working smoothly
Ways to manage more complex supply chains
Way | Explanation | Example |
---|---|---|
Use live data to trace every item |
|
|
Predict problems with artificial intelligence (AI) |
|
|
Increase transparency for consumers and investors |
|
|
Share IT platforms and paperwork digitally |
|
|
Monitor operations with connected sensors |
|
|
Influences on the choice of suppliers
Businesses often go to great lengths to find suitable suppliers of raw materials and components
Factors including the price, quality and reliability of supplies determine whether a business can efficiently produce high-quality products at a reasonable cost
There are several factors that can influence the supplier chosen by a business
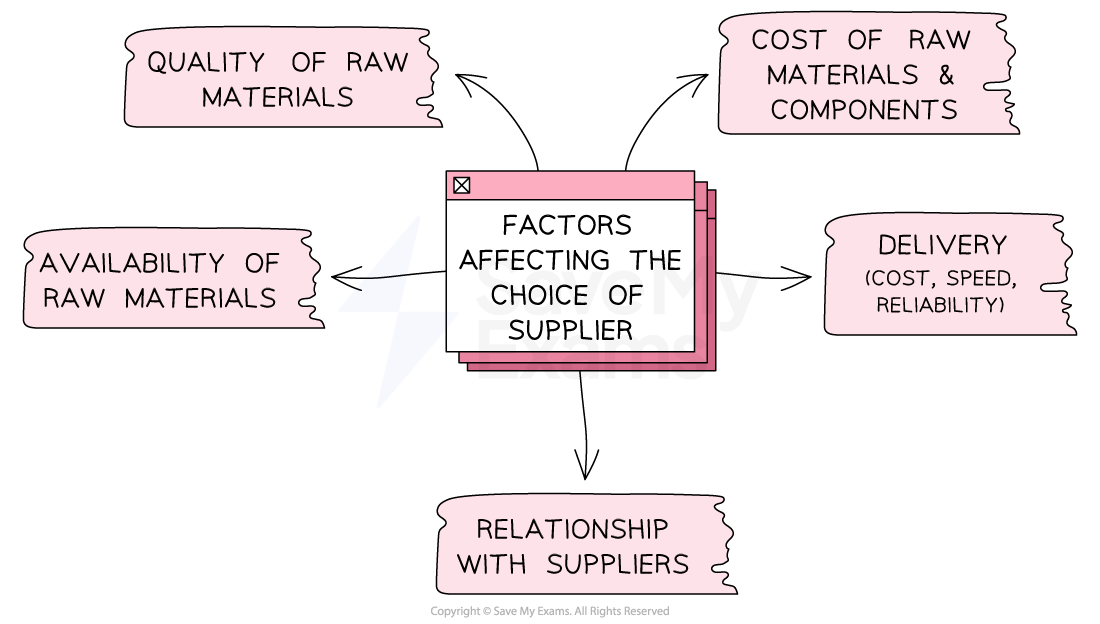
Factors that guide the choice of supplier
Factor | Why it matters |
---|---|
Quality |
|
Delivery reliability |
|
Availability and supply security |
|
Price and payment terms |
|
Ethical and sustainability standards |
|
Relationship and trust |
|
Flexibility and responsiveness |
|
Examiner Tips and Tricks
Explain why reliability might outrank price for JIT firms, but price could still dominate for cost‑leaders
Weigh at least two factors before choosing a supplier to reach evaluation marks
The value of outsourcing
Outsourcing is the process through which a business delegates specific business activities (IT, customer support, HR, etc.) to external service providers
Businesses choose to outsource these functions to reduce costs, access specialised expertise or focus on core competencies
Advantages of outsourcing
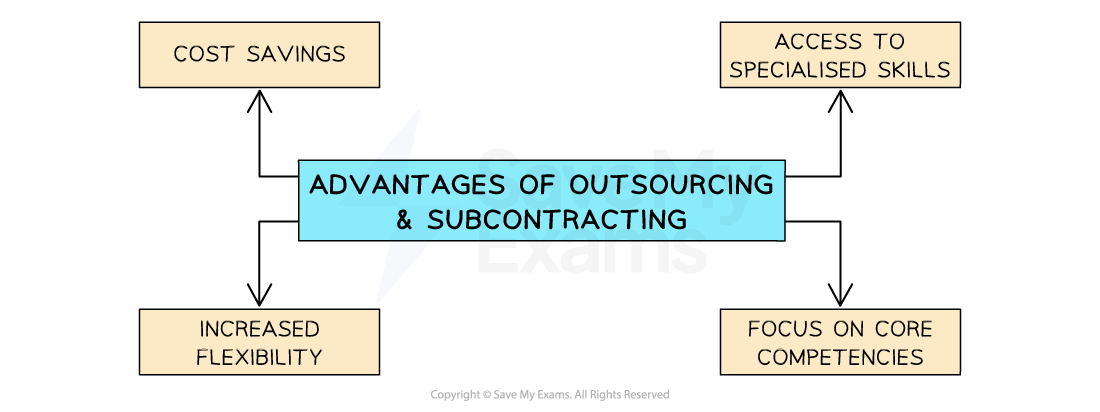
Cost savings
Businesses can often reduce expenses associated with operations such as hiring and training employees, maintaining infrastructure and managing IT systems
Access to specialised skills
External specialists have resources that the business lacks internally, which allows it to benefit from the knowledge and experience of industry specialists as and when required
Increased flexibility
Businesses can provide greater flexibility to scale their operations up or down based on demand fluctuations, which is particularly valuable in industries with seasonal or unpredictable demand
Focus on core competencies
Businesses can concentrate their resources and efforts on their core competencies, where they can add value
Limitations of outsourcing
Quality control
Using external providers makes it harder to ensure consistent quality and adherence to company standards
Loss of control
Handing direct control over those activities to others outside of the business may be risky
Companies must carefully select reliable partners and establish clear contractual terms to protect their interests
Data security and confidentiality
Sharing sensitive information outside of the business introduces potential risks to data security and confidentiality
Communication and cultural differences
Using global providers may result in language barriers or problems with time zone differences
Cultural differences may present communication challenges
Unlock more, it's free!
Did this page help you?